WJE PROJECTS
Port of Houston Woodhouse Grain Elevator
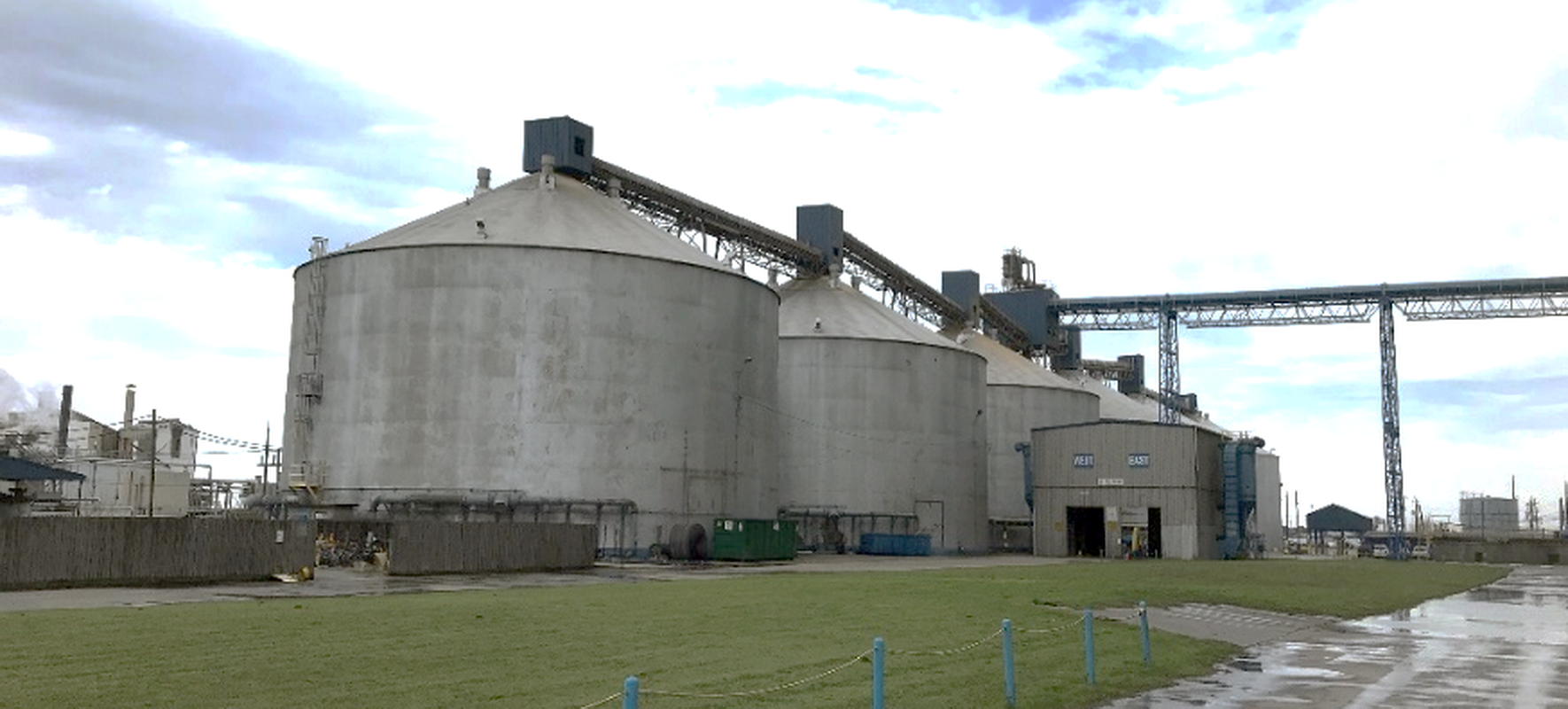
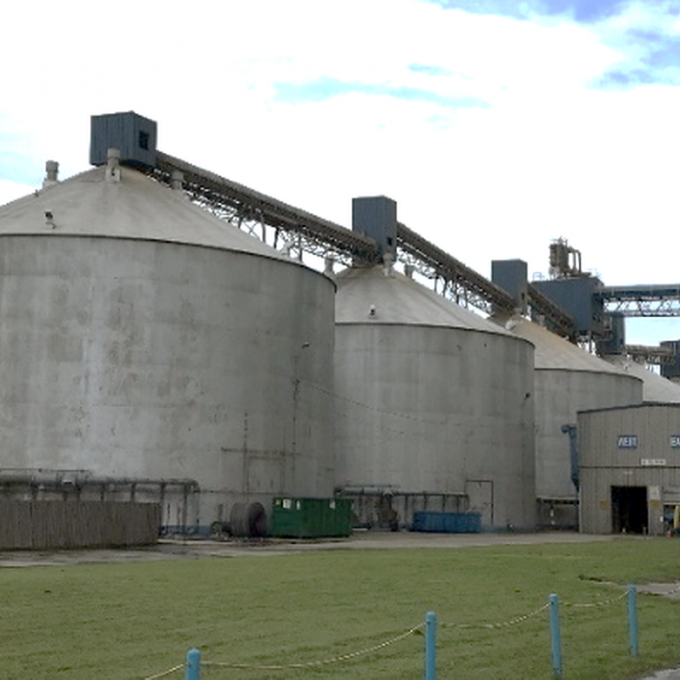
CLIENT |
Port of Houston Authority (PHA) |
LOCATION |
Galena Park, TX |
Condition Assessment and Cost Estimation
The WJE team, which included subconsultants for electrical and mechanical engineering as well as cost estimation, was retained to perform a due diligence inspection and condition assessment of the grain elevator and related structures and systems at the Port of Houston in Galena Park, Texas. The objective was to establish the current condition of the different terminal components and systems, as well as determine the need for repair or replacement at present and over the next thirty years.
BACKGROUND
The Woodhouse Grain Elevator Terminal, owned by the PHA, is located on a one-hundred-acre tract on the Houston Ship Channel. The grain elevator is located on the terminal’s Wharf 4 and was constructed in 1977 to replace the original grain elevator, which was destroyed in an explosion in 1976. The current grain elevator is a bulk export facility consisting of two concrete grain elevator buildings, concrete grain silos, steel grain storage tanks, truck and rail receiving facilities, and a T-head wharf.
SOLUTION
WJE’s specific scope included concrete grain elevator buildings, silos, and related structures, as well as steel bridge structures and storage tanks. Our due diligence assessment of the terminal concrete and steel structures was conducted primarily by visual observations. Given the size and nature of the steel structures, the inspections were performed by members of our Difficult Access Team, which used industrial rope access techniques. To efficiently assess the exterior of the 230- and 260-foot-tall grain elevator buildings, we surveyed the buildings using drone-mounted high-resolution video cameras to characterize and quantify the distress observed. The assessment involved five specialized WJE teams, in addition to subconsultant teams, to investigate the bulk materials handling systems and electrical and control systems in the terminal. The assessments were performed while the facility was operational and required careful planning and coordination with the PHA and terminal operator.
We developed repair or replacement recommendations for conditions requiring immediate action in addition to those anticipated to require action over the next five to thirty years. Cost estimates were prepared for construction consistent with Class 5, Concept Screening Level, as defined by AACE International. The project outcome was a schedule of recommended actions with associated cost estimates over a thirty-year period to support the strategic asset management needs and property leasing of the PHA.
RELATED INFORMATION
-
Our professionals deliver practical repair and rehabilitation services that maximize the... MORE >Services | Repair and Rehabilitation
-
We employ our industrial rope access team or drone capabilities to provide clients a solution to... MORE >Services | Difficult Access and Drone Survey
-
MORE >Markets | Marine Infrastructure
-
We apply the lessons learned from more than 175,000 projects to provide clients with a full... MORE >Services | Condition Evaluation